Warehouse Equipment: Building the Backbone of Australia’s Modern Supply Chain
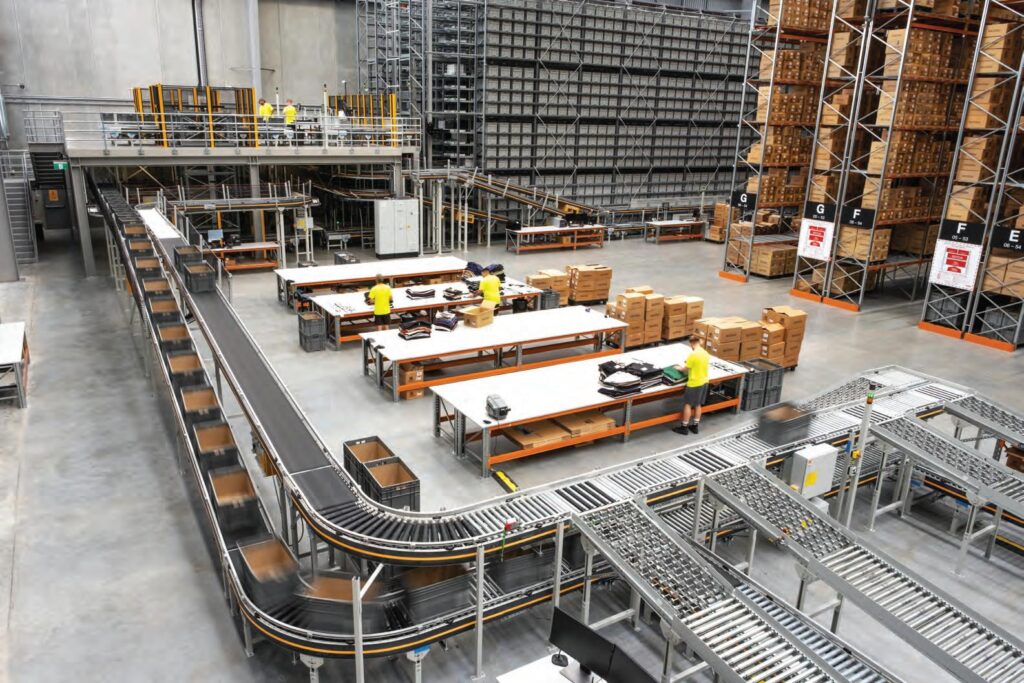
Walk into any bustling distribution center in Sydney or a chilled-goods warehouse on the outskirts of Perth and you will see a carefully choreographed dance of machinery, storage systems, and people.
Warehouse equipment is far more than forklifts and pallet racking; it is the invisible infrastructure that keeps Australia’s economy moving, allowing businesses to receive, store, pick, pack, and dispatch goods with speed and accuracy. From the rise of e-commerce to the growing demand for same-day delivery, the quality and suitability of warehouse equipment can decide whether an organization delights its customers or slips behind its competitors.
The Role of Warehouse Equipment in Modern Supply Chains
Supply chains have always relied on physical assets, but today’s Australian networks face unprecedented pressure for speed, transparency, and resilience. Warehouse equipment from castors2go provides the critical link between inbound freight and last-mile distribution. Well-chosen pallet jacks, conveyors, shelving, and safety systems cut handling times, improve stock accuracy, and reduce the risk of injury. In turn, these gains lower operational costs and help businesses adapt quickly to fluctuations in demand—whether that is a Black Friday rush or an unexpected surge in fresh-produce orders caused by a heatwave. Equipment choices now influence sustainability targets too, as companies measure energy consumption, emissions, and recyclability across every step of their supply chain.
Material Handling Basics: Pallet Jacks, Forklifts, and Beyond
Australian warehouses still lean heavily on manual pallet jacks, electric walkie stackers, and counter-balance forklifts as their material-handling workhorses. A pallet jack’s low cost and minimal maintenance make it ideal for narrow aisles, but electric high-reach trucks extend storage vertically, maximising cubic capacity as land prices rise in cities such as Melbourne and Brisbane. Articulated forklifts, sometimes called VNA (very narrow aisle) trucks, steer through aisles less than two metres wide, allowing operators to retrieve pallets stacked eleven metres high without turning the vehicle. Meanwhile, order-picker trucks with elevating platforms give staff direct access to individual cartons, supporting the growth of each-pick e-commerce orders. Selecting the right mix of equipment requires analysing throughput, SKU profiles, and shift patterns—a task often supported by simulation software that tests traffic flow under peak loads.
Storage Solutions: Racking Systems, Shelving, and Mezzanines
Storage is the silent engine room of the warehouse. Selective pallet racking remains Australia’s most common system because it offers immediate access to every pallet, but high-density alternatives such as drive-in racking, pallet flow lanes, and push-back racking reclaim valuable floor space for fast-moving lines. For smaller items, long-span shelving and carton live-storage create pick-faces that reduce travel time and improve visibility. Many sites also install mezzanine floors to double usable square metreage without costly building extensions, a popular strategy in land-constrained suburbs like Botany or Laverton North. Whether steel-framed or free-standing, mezzanines must comply with the National Construction Code and relevant Australian Standards for load capacity and fire egress—an important reminder that storage equipment is a structural asset as well as an operational tool.
Picking and Packing Stations: Ergonomic Design for Productivity
A well-designed pick-and-pack station can shave seconds off every order and protect staff from repetitive-strain injuries. Benches adjusted to elbow height, angled shelving, and footrests encourage a neutral posture, while LED strip lighting reduces eye strain during long shifts. Many Australian sites now integrate weigh-scales and dimensions directly into pack benches, allowing workers to print carrier labels in one motion from plastics2go. Touch-screen picking monitors, often running voice or scan-to-light software, direct staff to the correct SKU and verify quantities in real time. Importantly, every station must include anti-fatigue mats and easy-reach access to consumables such as void-fill paper and satchels. Investing in ergonomic furniture may seem minor compared with ordering a new forklift fleet, yet incremental gains at the workstation level compound across thousands of orders each day—boosting morale and reducing workers’ compensation claims.